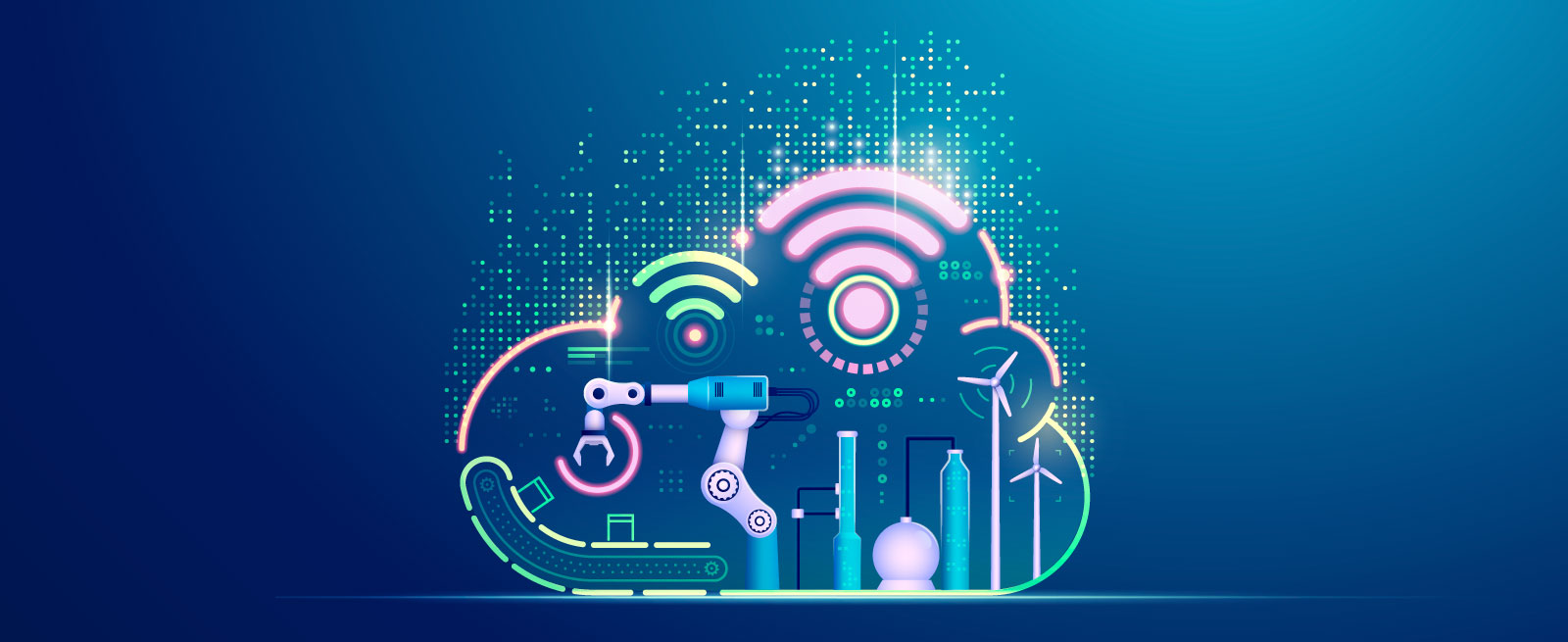
Material Requirements Planning
Material requirements planning entails establishing and managing a balanced manufacturing plan that incorporates master production schedules, sales forecasts, inventory levels, open orders, and bills of material.
Predictive Material & Resource planning
Predictive material and resource planning involves simulating production to evaluate material and capacity requirements.
Production Scheduling
Schedule and assign production orders to work centers, and plan shop floor setups and operations using a graphical planning board. This tool allows for visual management of production activities, enhancing efficiency and coordination.
Capacity Planning
Capacity planning entails allocating resources to balance workload and scheduling production steps in manufacturing. This involves ensuring that the right resources are available at the right time to meet production demands efficiently.
Manufacturing Operations
1. Production Execution
Production Execution involves controlling, monitoring, and automating manufacturing operations to enhance production schedules.
2. Production Control
Production control involves control in handling materials, parts, and assemblies from initial to finished-product stages.
3. Production Insights
Manufacturing analytics involve measuring operational performance to react quickly with the necessary adjustments.
See also the benefits of utilizing SAP S/4 HANA in